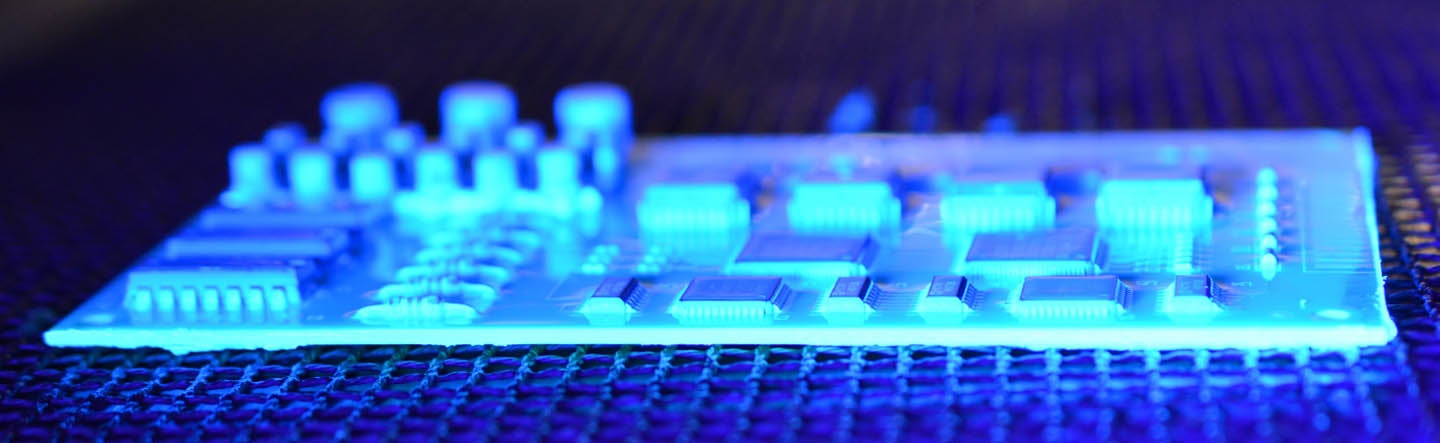
Conformal Coatings
The Leader in Conformal Coatings for Over 60 Years
Conformal coatings are essential for protecting electronic circuits from harsh environmental conditions such as high humidity, airborne contaminants, and fluctuating temperatures. By 'conforming' to the circuit board's topology, these protective layers provide electrical insulation, prevent corrosion, and maintain long-term surface insulation resistance (SIR), ensuring the operational integrity of your assemblies. At HumiSeal®, we’ve been at the forefront of conformal coating technology for over six decades. Recognized globally as a leader, we offer a full spectrum of solutions tailored to industries including aerospace, automotive (with a focus on hybrid and EV technologies), industrial controls, telecommunications, white goods, and energy (both traditional and renewable).
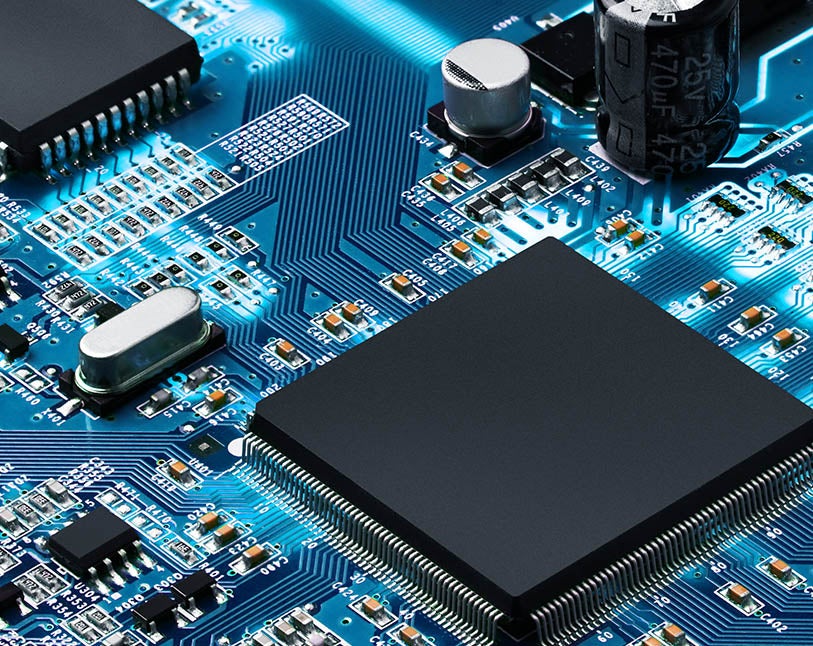
Conformal Coatings: Essential Protection for Printed Circuit Boards
Conformal coatings are crucial for protecting PCBs from environmental damage like moisture, dust, and extreme temperatures. These coatings provide electrical insulation, corrosion resistance, and increased durability, ensuring long-term reliability in demanding applications. Ideal for electronics, automotive, aerospace, and more, conformal coatings help extend the life of PCBs while minimizing the risk of failure due to environmental factors.
Conformal Coatings for every case
Acrylics
Acrylic coatings are popular for easy apply and remove, fast drying, fungus resistant long pot life. Low heat cure, low shrinkage, and robust humidity protection.
Urethanes
Single & two-component polyurethanes offer top humidity & chemical resistance. Heat-curing options vary with single or 2 component.
Synthetic Rubbers
Synthetic Rubber coatings have low glass transition temps, offer extreme flexibility, low moisture permeability, and stable performance across temperatures.
UV Curable
HumiSeal’s UV curable coatings offer fast curing, 100% solids, superb adhesion, and high flexibility for max production cycles.
Silicones
Silicone conformal coatings excel in high temps, under-hood automotive applications, and dampening vibrations in harsh conditions.
Epoxies
Epoxies perform in the most challenging environments; cure fast, resist chemicals, insulate electrically, and bond to key substrates.
Thinners & Solvents
HumiSeal Thinners are specifically formulated to be used in conjunction with different coating chemistries. The appropriate Thinner is identified on the datasheet.
Strippers & Thinners
HumiSeal Strippers are specifically formulated to be used in conjunction with different coating chemistries. Refer to the Technical Datasheet for your specific coating.
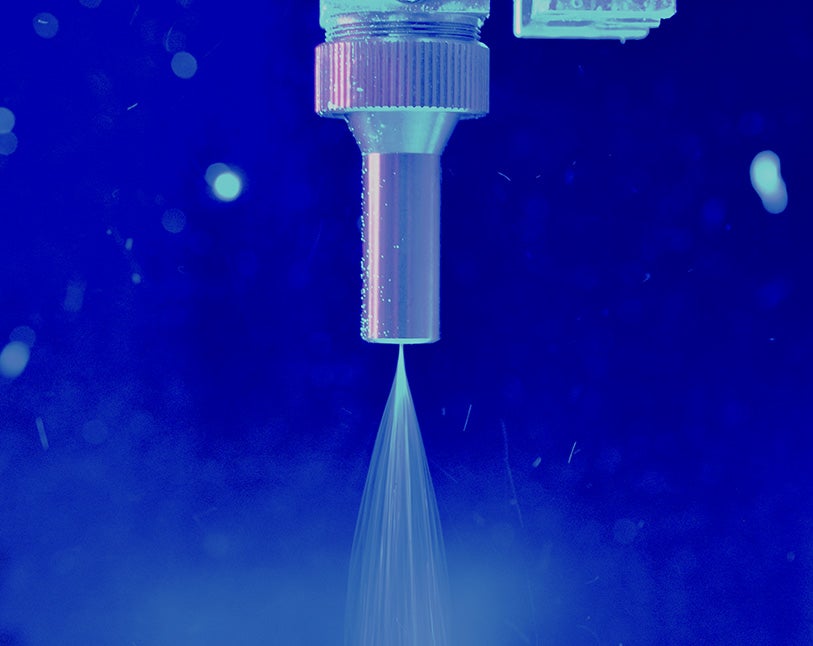
FAQ's
What is a Conformal Coating?
Conformal coating is a protective coating or polymer film 25-75µm thick (50µm typical) that ‘conforms’ to the circuit board topology. Its purpose is to protect electronic circuits from harsh environments that may contain high humidity, a range of airborne contaminants and varying temperatures. By being electrically insulating, it maintains long-term surface insulation resistance (SIR) levels and thus ensures the operational integrity of the assembly. It also provides a barrier to air-borne contaminants from the operating environment, such as salt-spray, thus preventing corrosion.
Conformal coatings are a breathable protective layer that will protect against the environment the PCA is exposed to by filtering out the airborne contaminants and maintaining long-term surface insulation resistance but will also allow any moisture trapped in the circuit board to escape.
The concept of a conformal coating of electronics was originally proposed and developed through research to meet the demanding requirements of the military decades earlier. HumiSeal was a part of that early research and has remained a pioneer and leader for over 60 years as the technology has expanded to an array of industries today including:
- Aerospace
- Automotive, including Hybrid and EV
- Industrial Controls
- White Goods
- Telecoms
- Energy both Traditional and Renewable
What are the Different Types of Conformal Coatings?
Conformal coatings come in a wide range of forms. From a physical standpoint, conformal coatings are commonly dispersed in organic solvents (solvent-based) or supplied in high or 100% solids (silicones and most UV curables).
From a chemical standpoint, conformal coatings’ standard chemistries include:
Acrylics
Acrylic conformal coatings are perhaps the most popular of all conformal coating materials as they are easy to apply and remove, with a wide process window for use. Acrylic coatings dry rapidly, are fungus resistant and provide long pot life. Additionally, acrylic materials produce little or no heat during the curing process, eliminating potential damage to heat sensitive components. The coatings possess low shrinkage, provide significant humidity resistance and exhibit low glass transition temperatures.
Urethanes
Polyurethane coatings are available in either single or two-component formulations. Both options provide excellent humidity resistance and far greater chemical resistance than acrylic coatings. Single component polyurethanes, while easy-to-apply and enjoy long pot life, sometimes require long curing regiments to achieve a full or optimum cure. In some instances, the cure cycle can be accelerated with the application of heat. Two-component formulations can reach optimum cure properties in as little as one to three hours with the assistance of heat.
Silicones
Silicone conformal coatings are most widely used in high-temperature environments due to their innate ability to withstand prolonged exposure to higher temperatures than most other conformal coating chemistries. This attribute has made them the primary choice for under hood automotive applications. They are also capable of being applied in thicker films making them useful as a vibration dampening/isolation tool if the coated assembly is to be placed in a high vibration environment.
Synthetic rubbers
HumiSeal’s Synthetic Rubber products are unique formulations that may enable the user to achieve specific protection / environmental goals not offered by “traditional” coatings. Synthetic Rubber materials are characterized by extremely low glass transition temperatures, resulting in stable modulus over a wide temperature range and extreme flexibility. Synthetic Rubbers have the least moisture permeability of all resins currently available. These products do not necessarily represent our complete Synthetic Rubber range.
UV curable acrylated urethanes.
HumiSeal’s UV curable conformal coatings represent an exciting innovation that provides superior performance. When combined with extremely fast curing, allows for short cycle times and maximum production speeds. These products can be sprayed using traditional automated spray equipment with the relatively simple addition of a small-footprint UV light curing unit.
Each chemistry is associated with certain physical properties that are suited for certain conditions and end-uses. For example, silicones tend to have the highest temperature resistance while synthetic rubbers and UV curables often provide the highest level of humidity resistance.
What Are the Advantages of Using a Conformal Coatings?
The advantages of conformal coatings can be summarized as follows:
- Insulating property allow a reduction in PCB conductor spacing of over 80%
- Can help eliminate the need for complex, sophisticated enclosures
- Light weight
- Completely protect the assembly against chemical and corrosive attack
- Eliminate potential performance degradation due to environmental hazards
- Minimize environmental stress on a PCB assembly
- Inherent flexibility conforms to varied component profiles\
Ideally, conformal coatings should exhibit the following characteristics:
- Simple application
- Easy removal, repair and replacement
- High flexibility
- Protection against thermal and mechanical shock
- Protection against environmental hazards
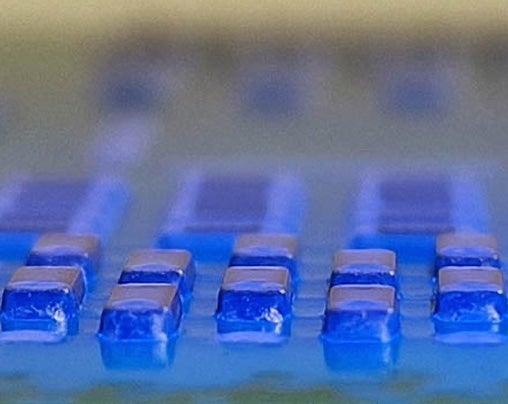
Sharp Edge Coverage: Ensuring Comprehensive PCB Protection
Sharp edges on printed circuit boards (PCBs) can lead to inconsistent conformal coating application and potential electrical failures. Effective sharp edge coverage ensures that the coating material is evenly distributed, even on highly detailed components. By addressing sharp edges, coatings maintain reliable insulation, prevent mechanical damage, and protect against corrosion in vulnerable areas. Proper application techniques, such as selective spraying or dipping, ensure thorough coverage, extending the longevity and reliability of the PCB.
Is Conformal Coating the Same as Waterproofing?
While conformal coatings offer moisture and humidity resistance, they are not fully waterproof. They allow trapped moisture to escape rather than sealing it inside. For applications requiring complete waterproofing, additional encapsulation techniques may be necessary. See our encapsulation solutions that make a material difference.
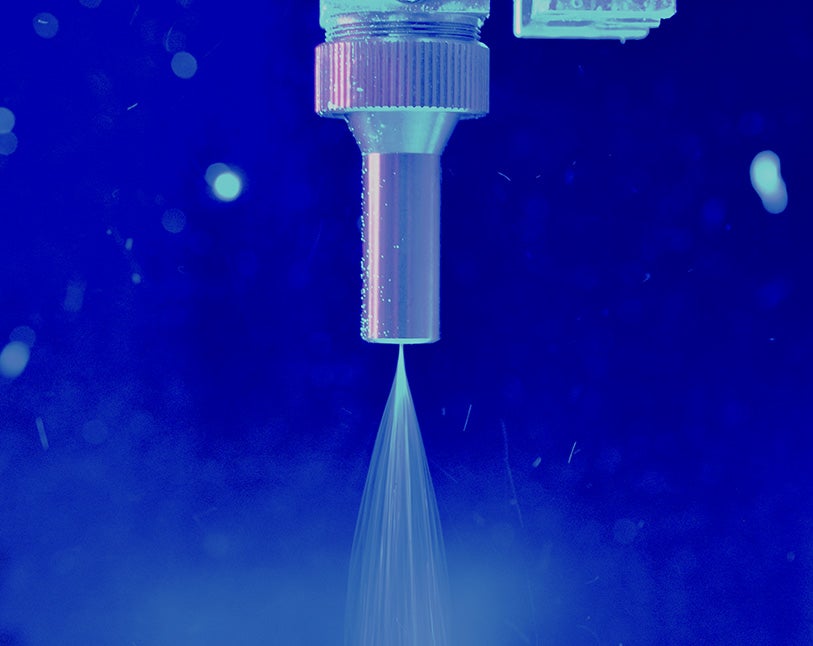
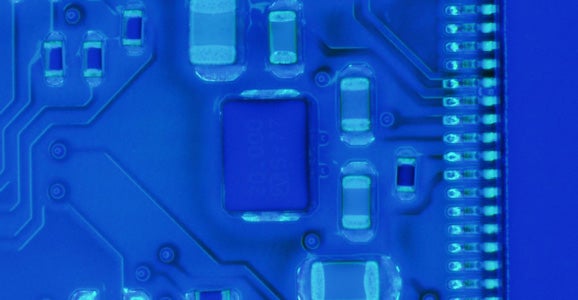
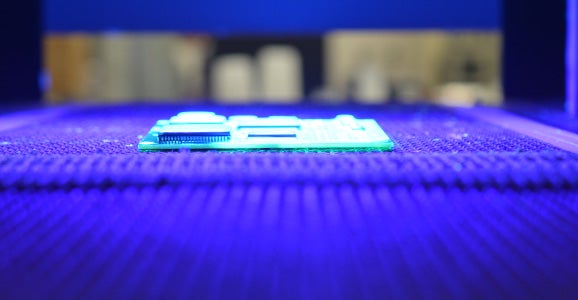