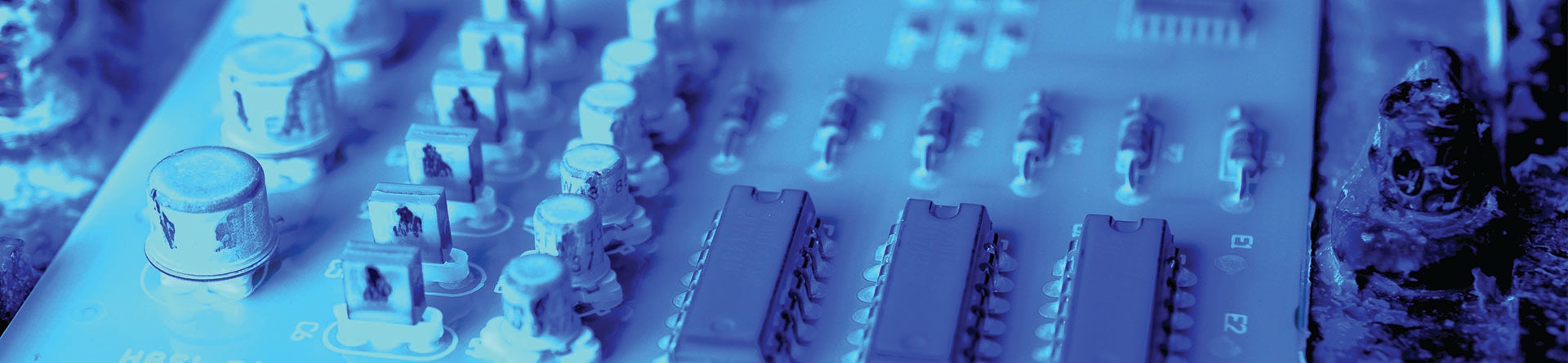
The Global Leader in Conformal Coating Technology
For over 60 years, HumiSeal has led the way in conformal coating technology, helping customers protect their electronic devices across various industries and environments. As pioneers in the field, HumiSeal consistently pushes the boundaries of performance, reliability, and efficiency. Their solutions safeguard critical electronics while offering cost-competitive advantages. Today, HumiSeal is celebrated for its technical leadership and unwavering commitment to enhancing production processes for customers worldwide.
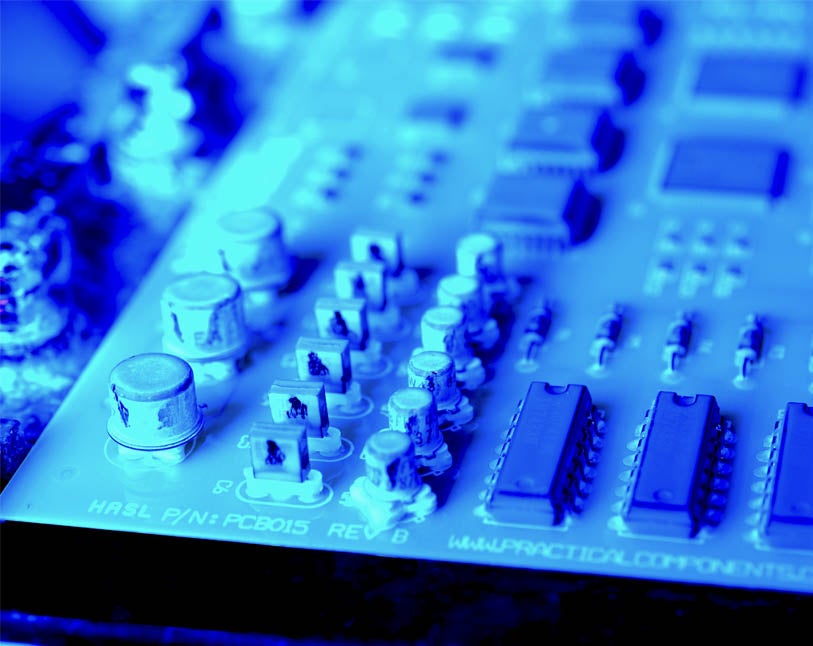
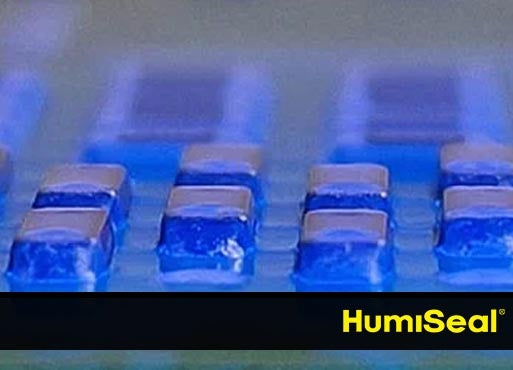
Sharp Edge Coverage (SEC) Technology
As PCBs shrink and components become more densely packed, traditional coatings struggle to adhere evenly to sharp edges, leading to weak spots, coating cracks, and reduced protection, compromising long-term reliability. HumiSeal’s Sharp Edge Coverage (SEC) Technology ensures uniform coating distribution, even on sharp corners and high-profile components. This breakthrough technology minimizes cracking, pooling, and uneven protection—delivering superior durability and long-lasting performance.
Moisture, Corrosion & Environmental Shielding
Moisture, humidity, and chemical exposure can degrade circuit boards over time, causing malfunctions, short circuits, and early product failure, especially in automotive, aerospace, and industrial environments. Our advanced conformal coatings form a reliable moisture and chemical barrier, shielding electronics from corrosion and harsh environmental conditions. With acrylic, silicone, urethane, and parylene options, we offer tailored protection for every operating environment—from humid climates to extreme temperature shifts.
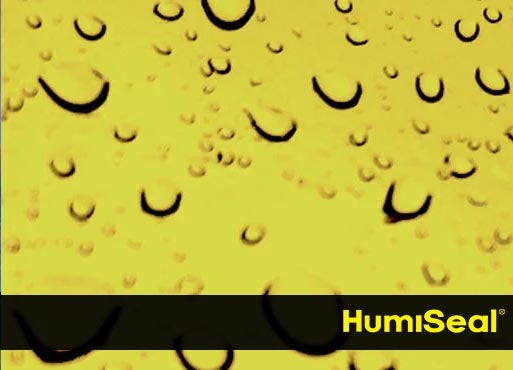
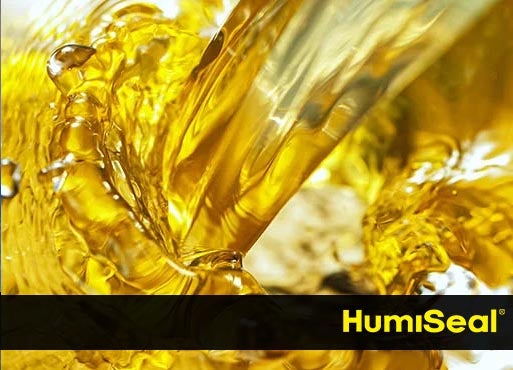
Optimal Viscosity and Flow Properties
Air bubbles, voids, and improper coating flow can create inconsistent protection, leaving sensitive components exposed to failure risks. HumiSeal’s coatings are formulated for optimal viscosity and flow properties, ensuring smooth, even distribution across components. Our UV-curable coatings solidify quickly, reducing bubble formation and delivering flawless, defect-free coverage for high-reliability electronics.
UV-Curable and Fast-Drying Coatings
Traditional coatings can take hours or even days to fully cure, slowing down manufacturing efficiency and increasing costs for high-volume production. Our UV-curable and fast-drying coatings dramatically reduce cure times, allowing manufacturers to increase throughput without compromising quality. UV coatings provide instant curing under UV light, making them ideal for high-speed production environments.
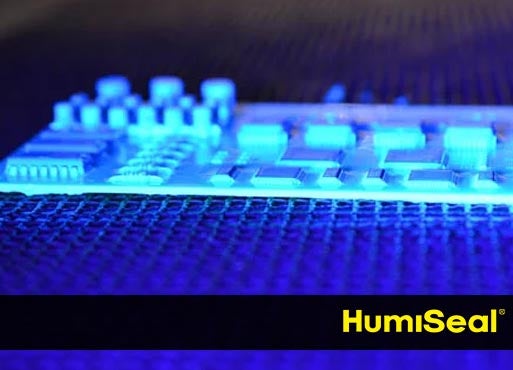
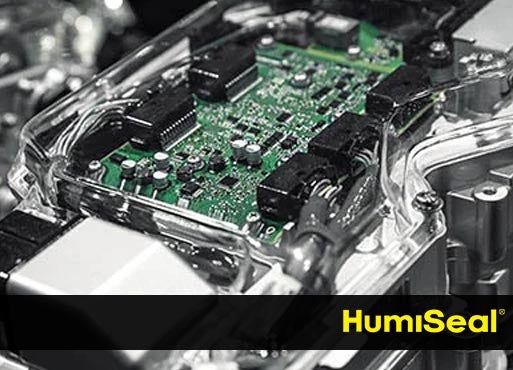
Tailored Coatings for Unique Applications
Selecting the wrong coating for your electronic device can lead to performance failures and costly redesigns. HumiSeal offers all major coating chemistries and works directly with customers to develop custom formulations tailored to their exact requirements. Whether you need high-flexibility silicone, ultra-thin Parylene, or high-durability urethane coatings, our experts help select the perfect solution for your application.
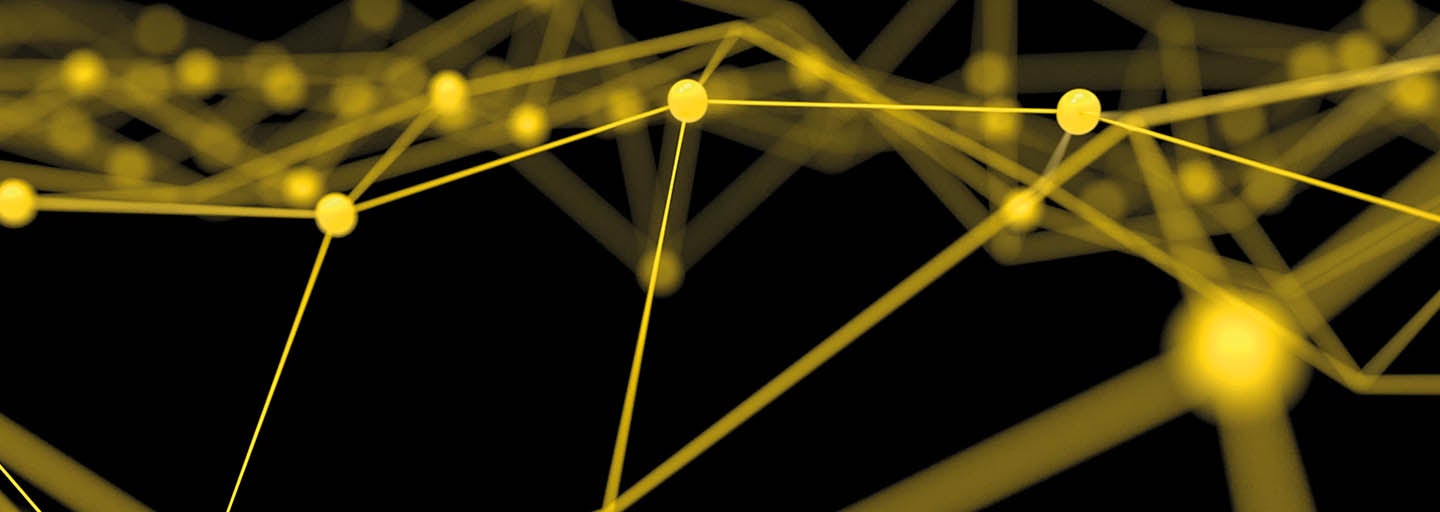
Partner With Us for Tailored Solutions
The HumiSeal team specializes in the research, development, and manufacture of conformal coating, thermal management, potting, encapsulating and specialty adhesive products. All which serve a variety of industries.
The product offering includes:
- Acrylics | Urethanes | UV Curable Products | Silicones | Synthetic Rubbers
HumiSeal materials are used for the protection of electronic and industrial devices against humidity, moisture, surface contaminants, mechanical and thermal stresses, as well as UV and chemical exposure.
We encourage customers to partner with us in developing products that are tailored to their exact requirements.
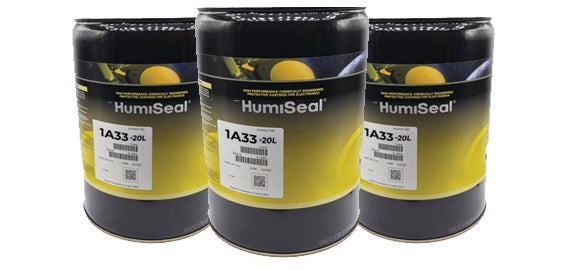
Shop Products
Browse over 900 products across the many brands in the Chase Corp family. See firsthand how Chase makes a material difference.
Shop now >See all Markets
Chase products are used across a wide range of industries. See how our solutions have grown to influence sectors all over the world.
Read more >