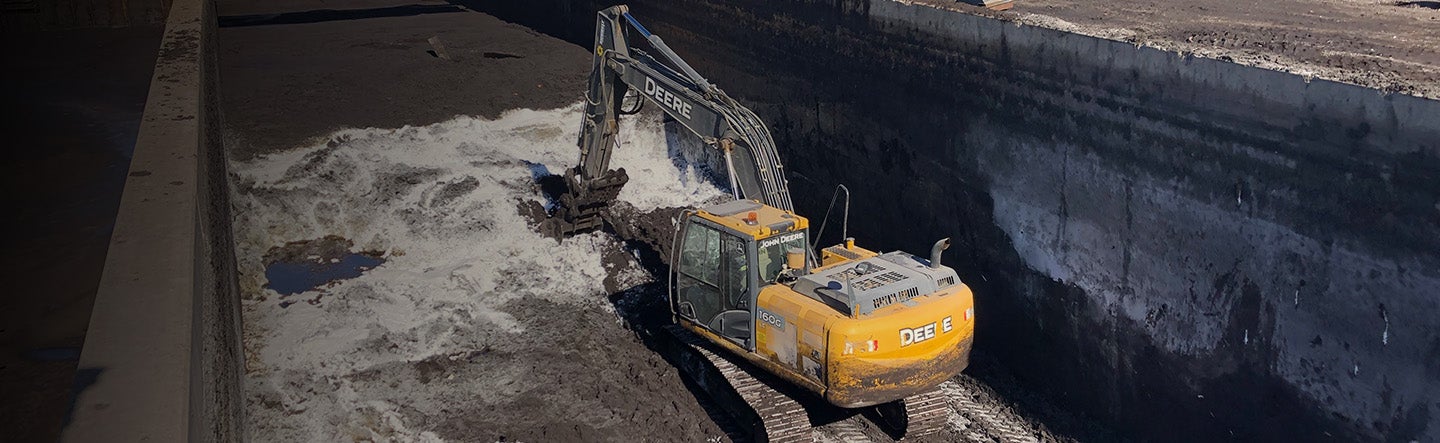
Solidifiers
Superabsorbent polymers (SAPs) are versatile materials engineered for superior liquid absorption and retention across diverse applications. From industrial spill control to medical waste management and environmental remediation, SAPs provide efficient, eco-friendly solutions tailored to specific needs.
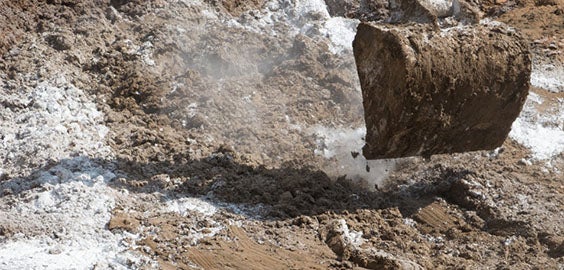
Superabsorbent Powder
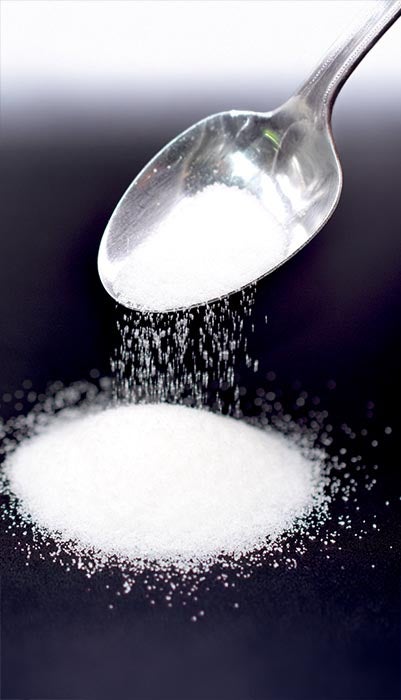
Managing Large Volumes with Low Dosage Rates
SAPs are designed to absorb tremendous volumes of fluid very quickly. With an absorption capacity 75x greater than sawdust, the efficiency and speed of liquid absorption with SAPs help environmental waste management professionals manage complex construction schedules and minimize risk.
The Industry-Leading Choice for SAP-Based Solidification
Zappa Stewart’s SAPs outperform traditional solidifiers by offering faster absorption, greater efficiency, and long-term stability. Designed to meet the toughest liquid control challenges, our SAPs provide a reliable and cost-effective solution.
Features and Benefits
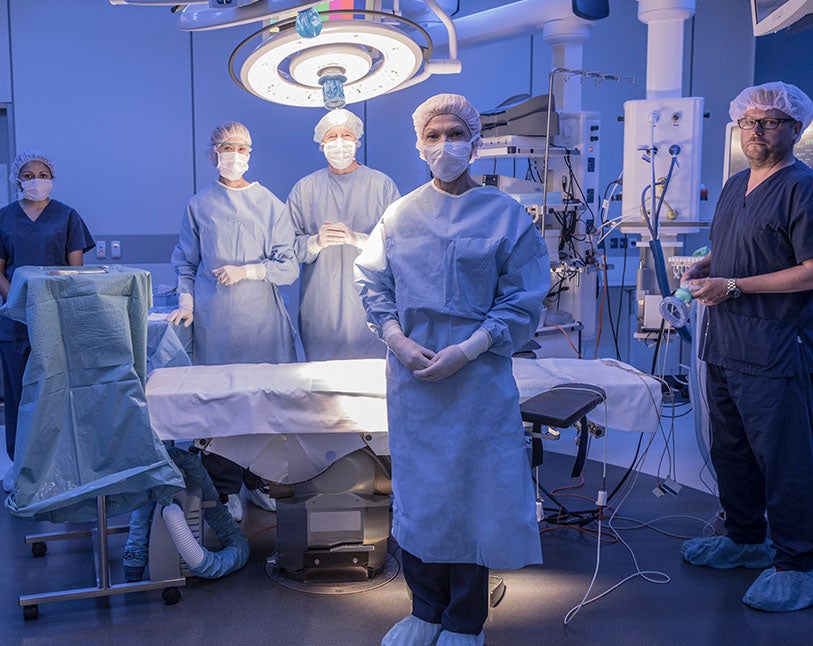
Maximizing Efficiency in Waste Solidification with SAPs
Liquid waste solidification is a critical waste management method across industrial sectors. When comparing solidification products, absorption capacity plays a key role in selecting the right solution. SAPs offer an absorption capacity up to 75 times greater than traditional materials.
Due to the logistical challenges and limited landfill disposal options for liquid wastes, transforming these materials into solid waste is a practical, cost-effective solution. SAPs provide a superior, efficient approach to solidification, reducing both material requirements and disposal complexities.
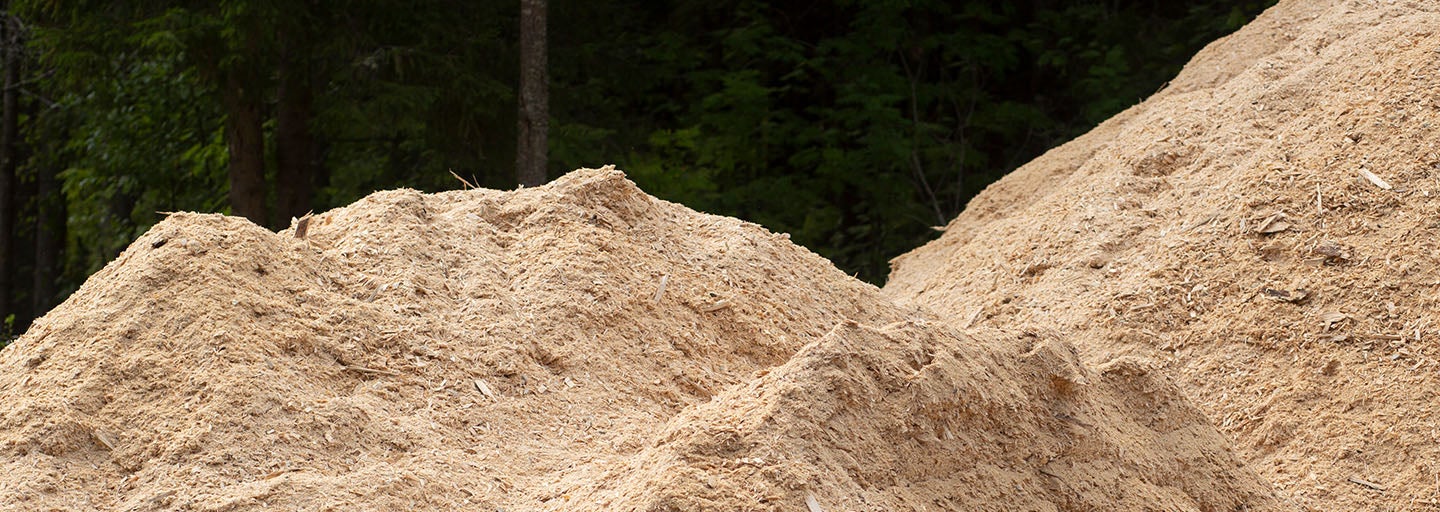
Zappa-Stewart has developed a series of lab tests and field demonstration tests that can allow contractors and engineers to determine the “best,” or optimized, mix for each site.
Minimizing the dosage rates of solidification media minimizes the amount of material to be shipped to the site, staged on-site, blended into the waste, and hauled to the landfill.
SAP, sawdust, or quicklime? Crunch your own numbers with our cost calculator